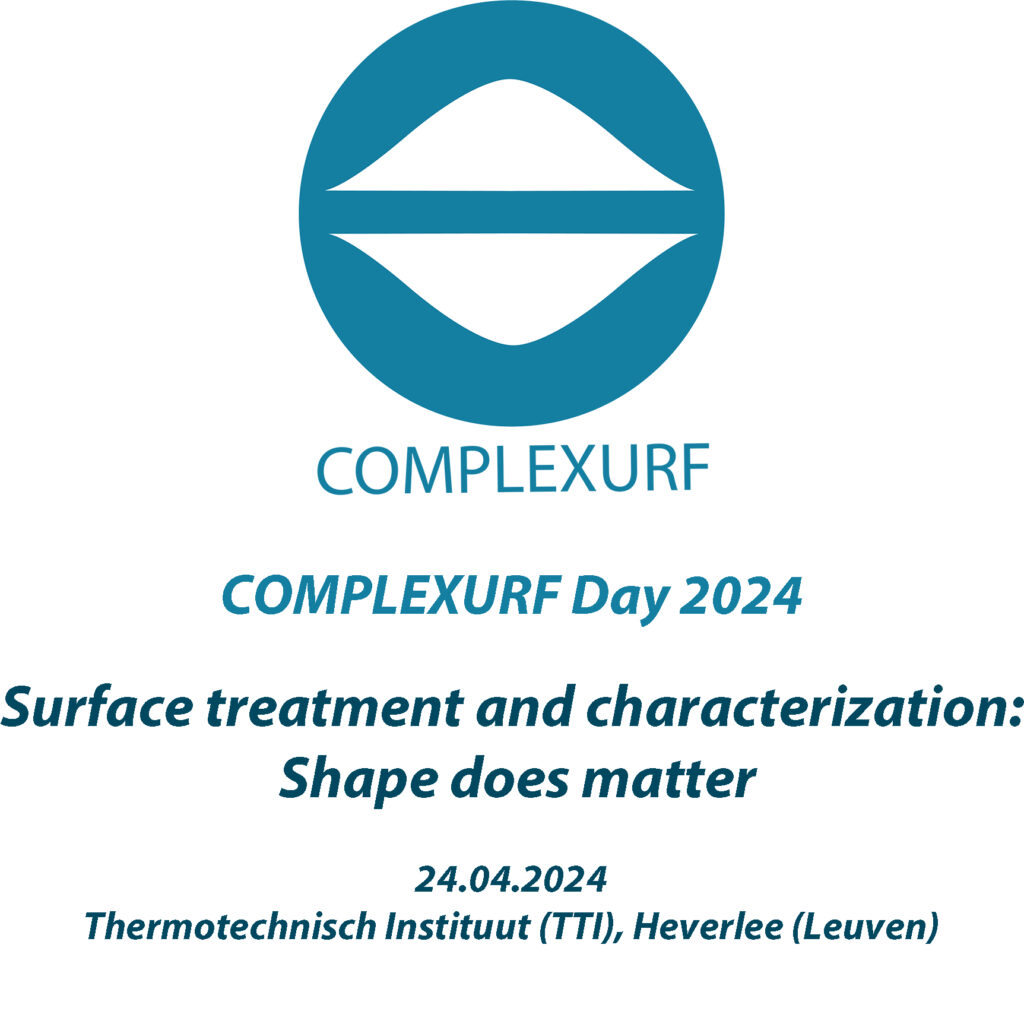
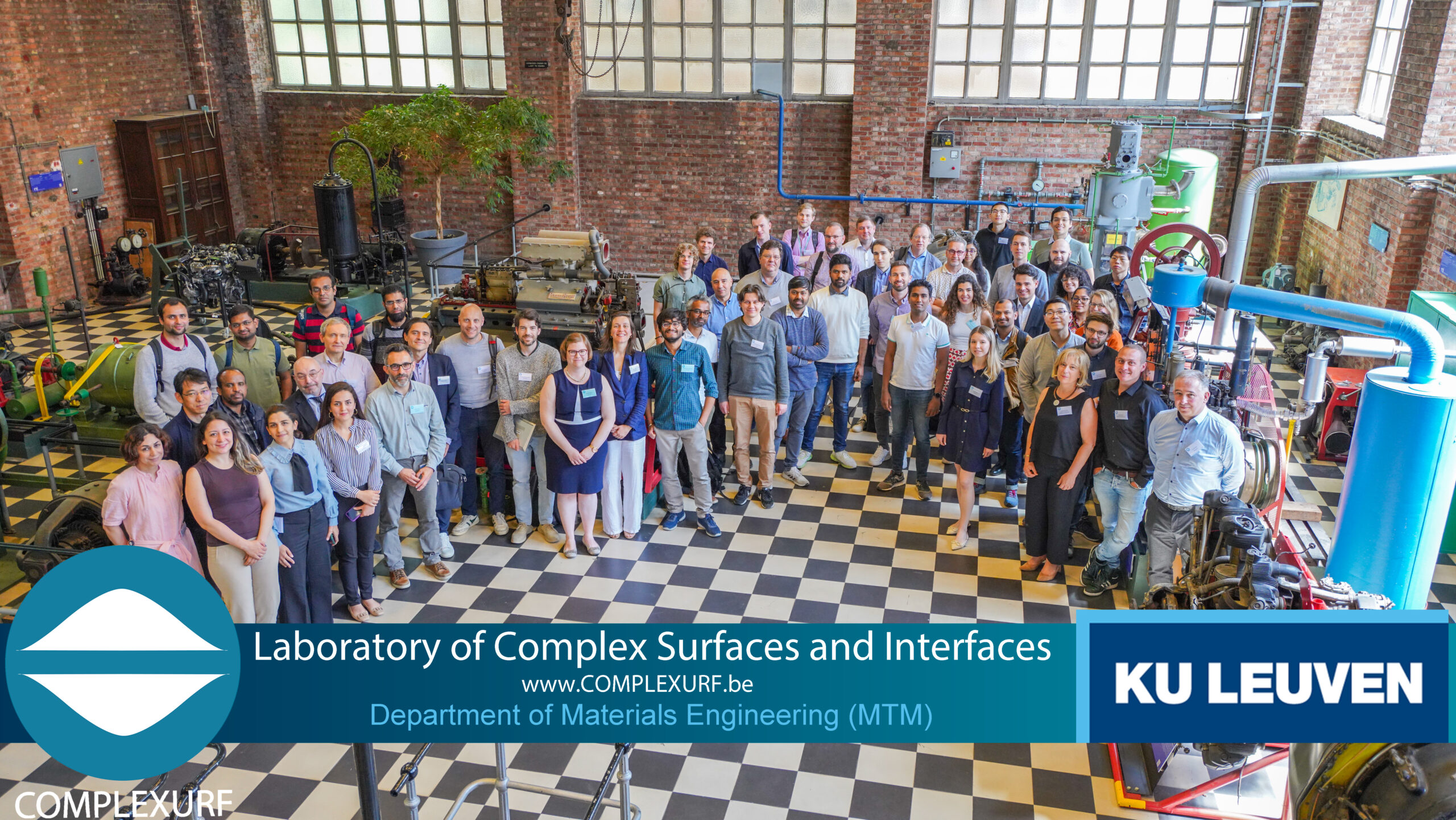
Laboratory of Complex Surfaces and Interfaces (COMPLEXURF) will organize the COMPLEXURF Day 2024 at KU Leuven Department of Materials Engineering (MTM) on April 24, 2024. The topic theme of this year’s event is “Surface treatment and characterization: Shape does matter” with talks from academia, research centers, and companies. The event will be held on site only at Thermotechnisch Instituut (TTI), Heverlee (Leuven).
The initial agenda of the event is:
Time | Presenter | Affiliation | Agenda point/presentation title |
---|---|---|---|
08:30-09:00 | ☕️ | ☕️ | Arrival/Coffee |
09:00-09:10 | David Seveno | KU Leuven | Welcome & Introduction |
09:10-09:40 | David Seveno | KU Leuven | What did the COMPLEXURF project do for us and could do for you? |
09:40-10:20 | Stijn Van Vrekhem | Centexbel | Advancements in Textile Functionalization and Surface Modification: Exploring National and International Research |
10:20-10:40 | ☕️ | ☕️ | Coffee break |
10:40-11:20 | Gilles Koolen | KU Leuven | A researcher’s path to entrepreneurship: Experiences from a biocomposite start-up |
11:20-12:00 | Rik Verschueren | Partix | Plasma Functionalization and Encapsulation of Particles as a Novel Coating Technology |
12:00-13:00 | 🥪 | 🥤 | Walking Lunch & Poster Session |
13:00-13:40 | Geert Deroover | Chemstream | A toolkit for pigment surface and morphology modification: tailoring the optical and physicochemical properties |
13:40-14:20 | Thomas Godfroid | Materia Nova | PVD solutions to coat objects with complex geometries |
14:20-14:40 | ☕️ | ☕️ | Coffee break |
14:40-15:40 | 🔬 | 🧪 | Lab Tour |
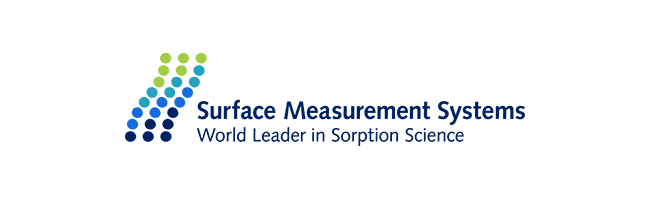
This event is sponsored by Surface Measurement Systems